
Xinnuo Sandwich Panel Production Line for EPS and Rock Woll
HEBEI XINNUO ROLL FORMING MACHINE CO., LTD.- After-sales Service:Door to Door
- Warranty:One Year
- Tile Type:Colored Steel
- Certification:CE, ISO, BV
- Condition:New
- Customized:Customized
Base Info
- Model NO.:Sandwich Panel Production Line
- Usage:Roof, Wall
- Transmission Method:Pneumatic
- Delivery:60days
- Voltage:308V 50Hz 3phases
- Weight:17.5 Tons
- After Sales Service:Engineers Available to Service Oversea
- Transport Package:by Sea
- Specification:4500mmx2500mmx2600mm
- Trademark:Xinnuo
- Origin:China
- HS Code:84552210
- Production Capacity:200 Set Per Year
Description
Overview
Product Description
Sandwich panel production line is especially designed for producing insulation composite board. With stepless speed regulation system, it is able to produce corrugated composite panel efficiently at one time. Sandwich panel roll forming machine has been an indispensable device in fabricating roof panels and wall panels in plants and warehouses, among other buildings.
Features
1. The motor power of the sandwich panel roll forming line is 4kw, and the production speed reaches 6m/min. With the stepless speed regulation system, the efficiency of the roll forming line is optional within 0-6m/min.
2. When producing EPS sandwich panel, the speed is generally controlled at 2-6 m/min. It will be slightly lower for making rock wool board (depends on actual needs)
3. The composite panel production line is equipped with K-9 glue metering pump, featuring low rotating speed and high accuracy. The glue is fed at a rate of 0.1-2.0 kg/min. It is controlled by frequency converter.
4. The thickness of the composite panel the roll forming unit can produce is varied from 50mm to 250mm. By adjusting the upper and lower rack, and the distance between the cutter holder and the material feeding rack, we can get sandwich boards with different thickness and specifications.
5. Total installed capacity: 34KW; total weight (including accessories): 17.5t.
6. Dimension of the panel roll forming machine: 12500 (16000 for rock wool boards) X2200X2800; the roll former for 5 type EPS sandwich panel adopts 23 rubber shafts and 160X80 square tubes with thickness of 6mm; the roll former for 7 type composite rock wool panel employs 45 rubber shafts, and upper and lower independent glue supply. It is equipped with 1.7m rock wool panel conveyor belt, with the diameter of the drive shaft to be 50mm; length of the machine frame is up to 9m; the roll former is welded with 180X80 square tubes which thickness is 8mm.
Requirements for Factories:
The factories where our EPS sandwich panel production line are applied can be either flatroof or sloped-roof type. The height of the cornice should be larger than 5m, and the effective width should be at least 45m. The floor of the factory should be flat and concrete. For foundation of the roll forming line, it is required to be to be 380V, and the total installed power is 34kw. It is necessary for the factory to be equipped with 0.4-0.6MPa compressed air supply and illumination devices. The roll forming machine shares the same power supply with the auxiliary devices. The fluctuation of voltage should be no more than 10%, or it may lead to an abnormal running of the system.
The stroke is no less than 29m, the load for a lifting process is larger than 5000kg, and the lifting height is no less than 3.9m. For daily production and maintenance, about 6-10 people are needed, with 3-4 operators for some core processes included.
Accessories List of 5 Type Composite Roof And Wall Cladding Panel Machineadjust spanner 3pieces filter element 2pieces big glue head 2pieces bulkhead glue 4pieces glue joint 4pieces steel sheet chuck 2pieces screw depends machine tool pad iron 16sets brake plate 3 sets M16×140 bolt 16pieces axes 1piece M16 nut 16pieces steel wire tube 1piece heating tube 8pieces heating tube ceramics end 16sets glue pipe 6pieces M8×35 inner hexagon screws 30pieces φ10×80 taper pin 1piece delivery rack 1set mainframe 1set cutting rack 1set tile plate wheel 1set overtravel-limit switch 2pieces pneumatic elements 1 set glue channel(4long 2short) 6pieces large tray 1piece ladder 1piece M16×40 outer hexagon screws 8pieces Color clip 4 sets discharge rack 1piece 05-06 frame 1set rod 12pieces 00 frame 1piece hanger 1piece 4 m foam holder 4pieces long cylinder 1piece clip lock lever 2pieces bourdon spring 1piece 1220 roller 8pieces roller axes 16pieces 6004 bearing 16sets M20 nut 24pieces cutting under frame 1 piece
Detailed Photos
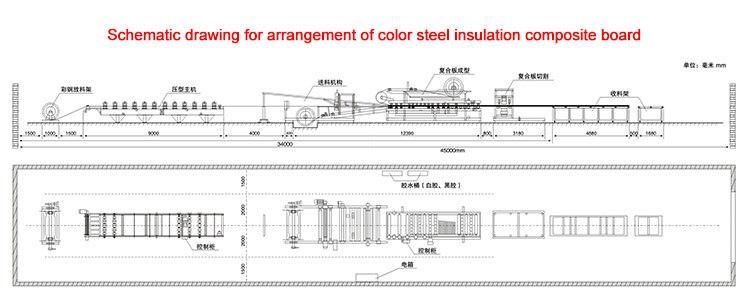
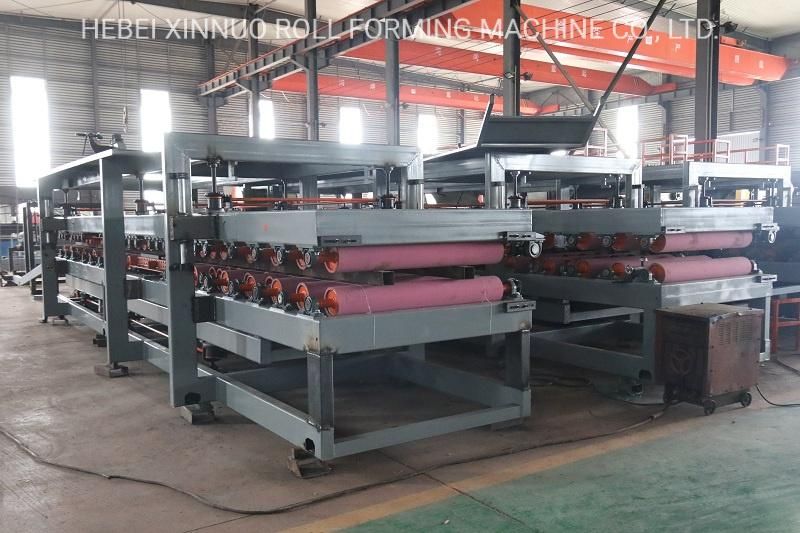
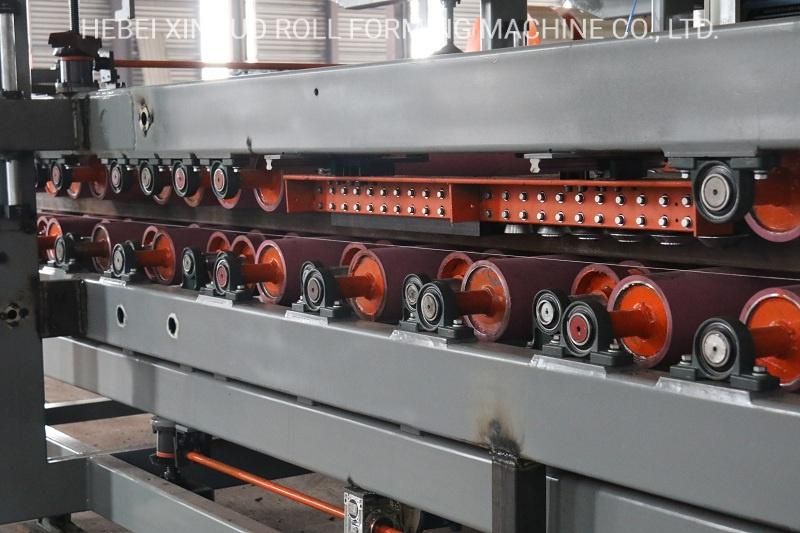
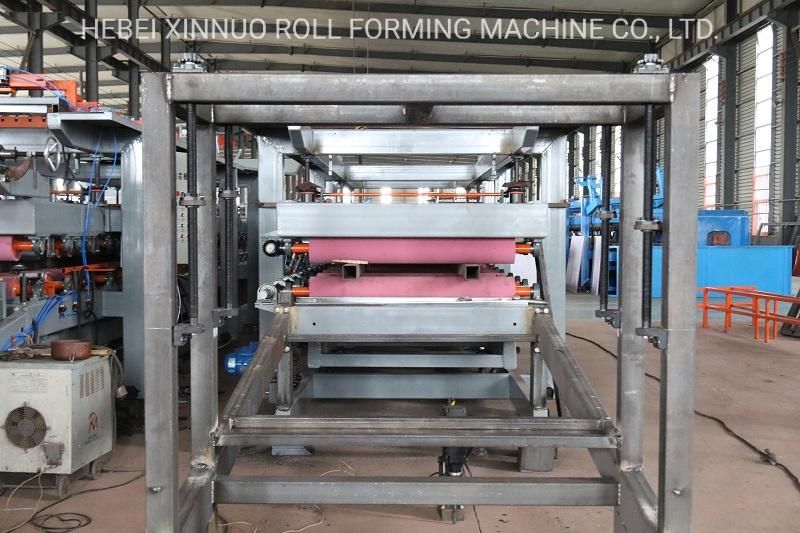
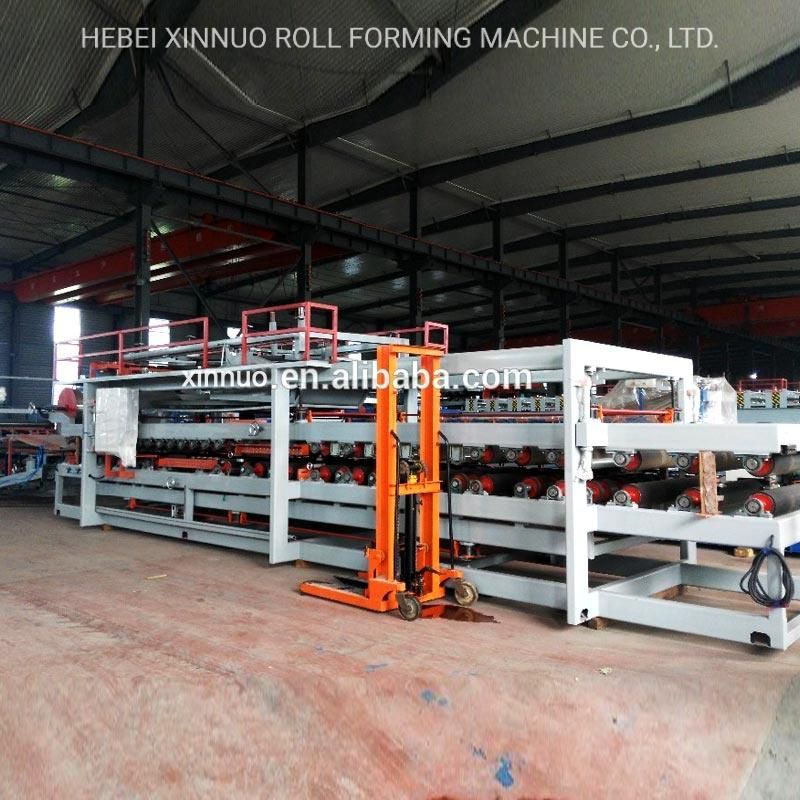
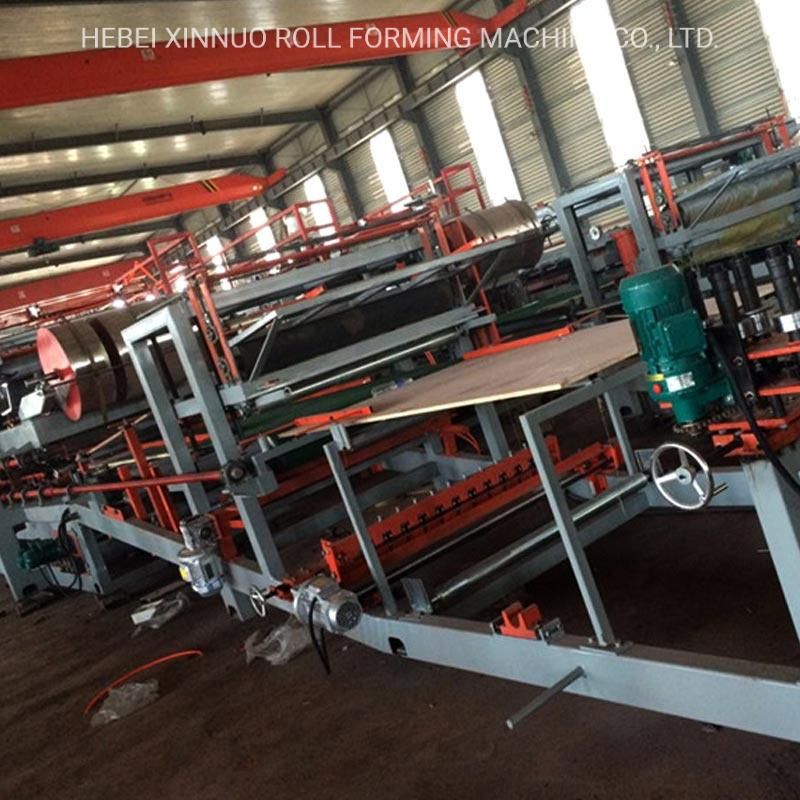
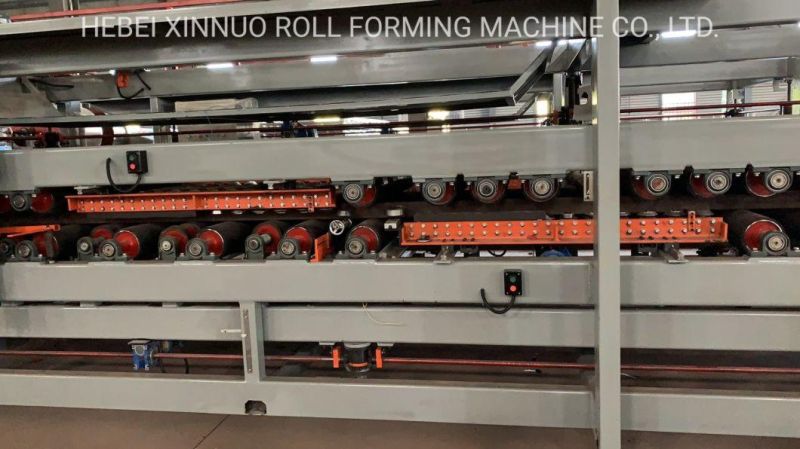
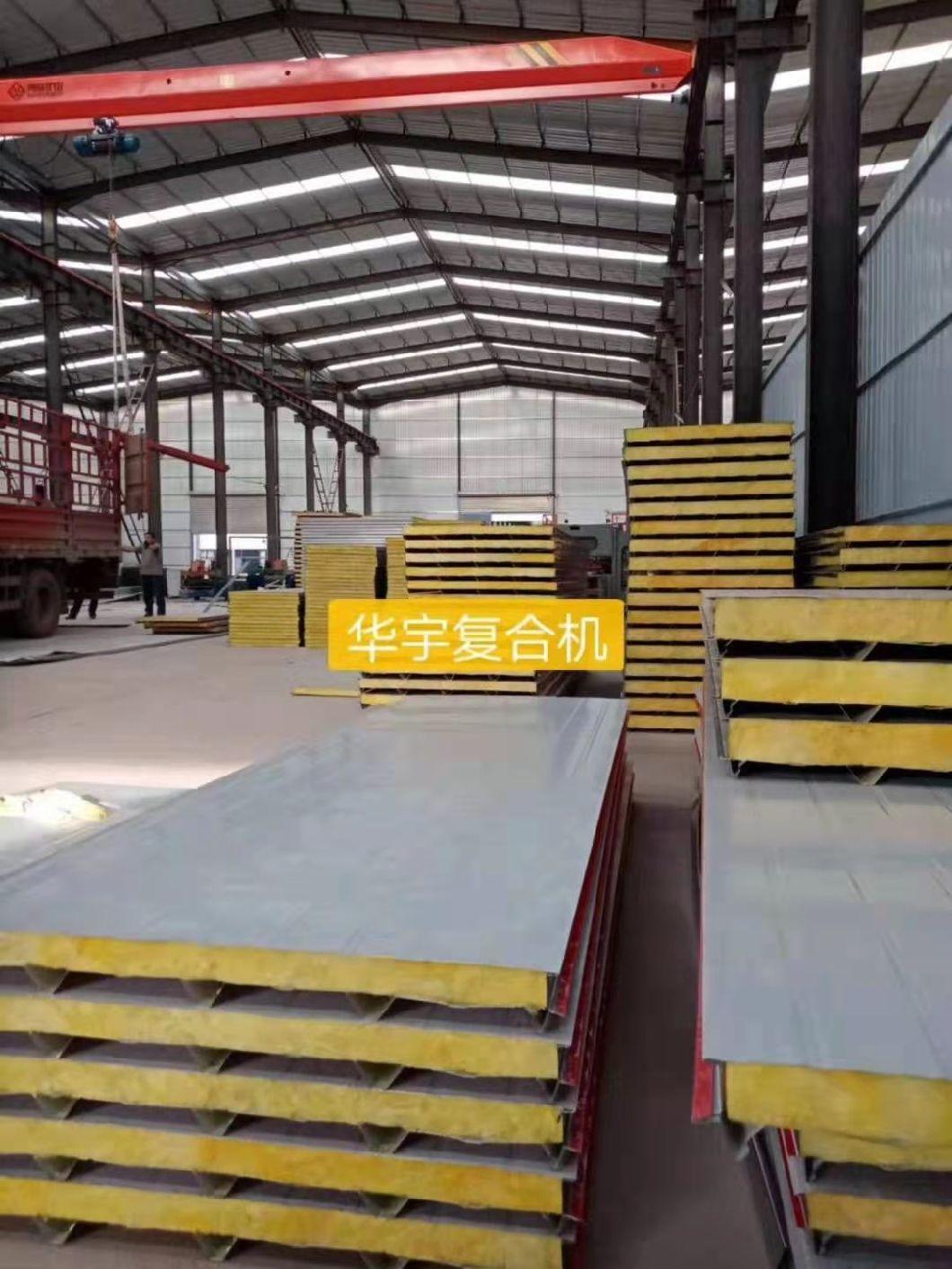
Our Advantages
Mineral Wool Sandwich Panel line, Sandwich Panel Roll Forming Line
Sandwich panel production line is especially designed for producing insulation composite board. With stepless speed regulation system, it is able to produce corrugated composite panel efficiently at one time. Sandwich panel roll forming machine has been an indispensable device in fabricating roof panels and wall panels in plants and warehouses, among other buildings.
Features
1. The motor power of the sandwich panel roll forming line is 4kw, and the production speed reaches 6m/min. With the stepless speed regulation system, the efficiency of the roll forming line is optional within 0-6m/min.
2. When producing EPS sandwich panel, the speed is generally controlled at 2-6 m/min. It will be slightly lower for making rock wool board (depends on actual needs)
3. The composite panel production line is equipped with K-9 glue metering pump, featuring low rotating speed and high accuracy. The glue is fed at a rate of 0.1-2.0 kg/min. It is controlled by frequency converter.
4. The thickness of the composite panel the roll forming unit can produce is varied from 50mm to 250mm. By adjusting the upper and lower rack, and the distance between the cutter holder and the material feeding rack, we can get sandwich boards with different thickness and specifications.
5. Total installed capacity: 34KW; total weight (including accessories): 17.5t.
6. Dimension of the panel roll forming machine: 12500 (16000 for rock wool boards) X2200X2800; the roll former for 5 type EPS sandwich panel adopts 23 rubber shafts and 160X80 square tubes with thickness of 6mm; the roll former for 7 type composite rock wool panel employs 45 rubber shafts, and upper and lower independent glue supply. It is equipped with 1.7m rock wool panel conveyor belt, with the diameter of the drive shaft to be 50mm; length of the machine frame is up to 9m; the roll former is welded with 180X80 square tubes which thickness is 8mm.
Requirements for Factories:
The factories where our EPS sandwich panel production line are applied can be either flatroof or sloped-roof type. The height of the cornice should be larger than 5m, and the effective width should be at least 45m. The floor of the factory should be flat and concrete. For foundation of the roll forming line, it is required to be to be 380V, and the total installed power is 34kw. It is necessary for the factory to be equipped with 0.4-0.6MPa compressed air supply and illumination devices. The roll forming machine shares the same power supply with the auxiliary devices. The fluctuation of voltage should be no more than 10%, or it may lead to an abnormal running of the system.
The stroke is no less than 29m, the load for a lifting process is larger than 5000kg, and the lifting height is no less than 3.9m. For daily production and maintenance, about 6-10 people are needed, with 3-4 operators for some core processes included.
Accessories List of 5 Type Composite Roof And Wall Cladding Panel Machine
Detailed Photos
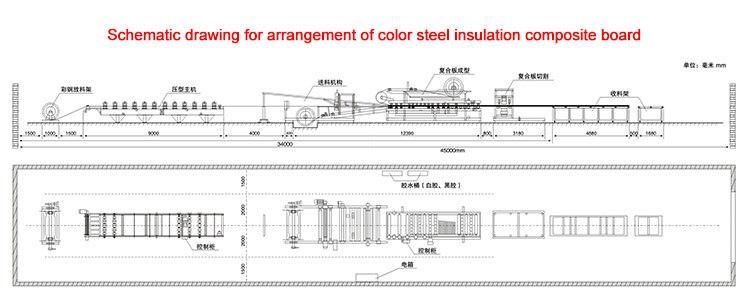
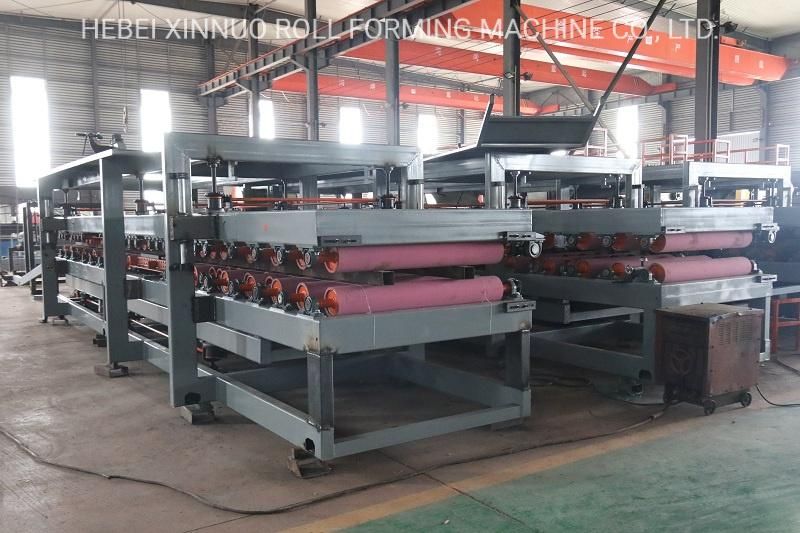
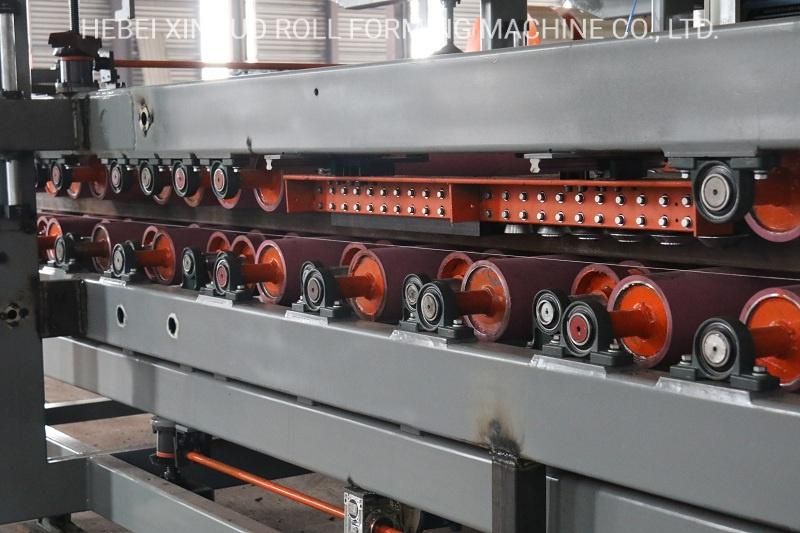
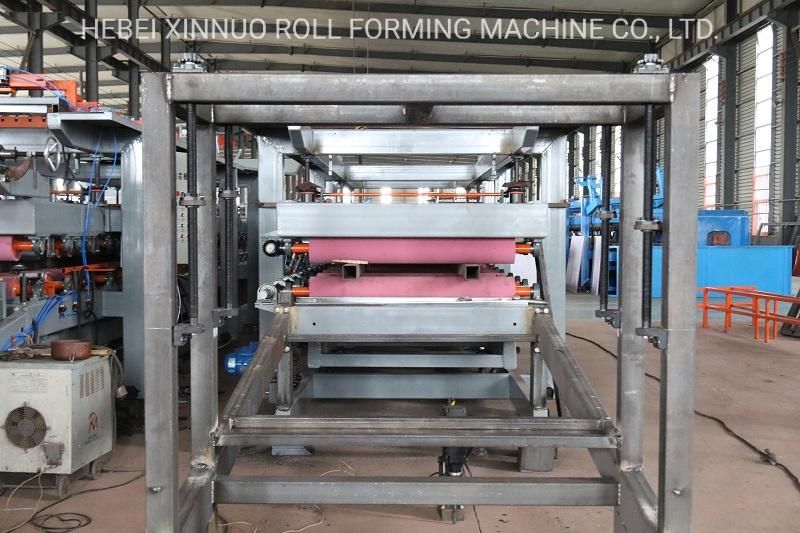
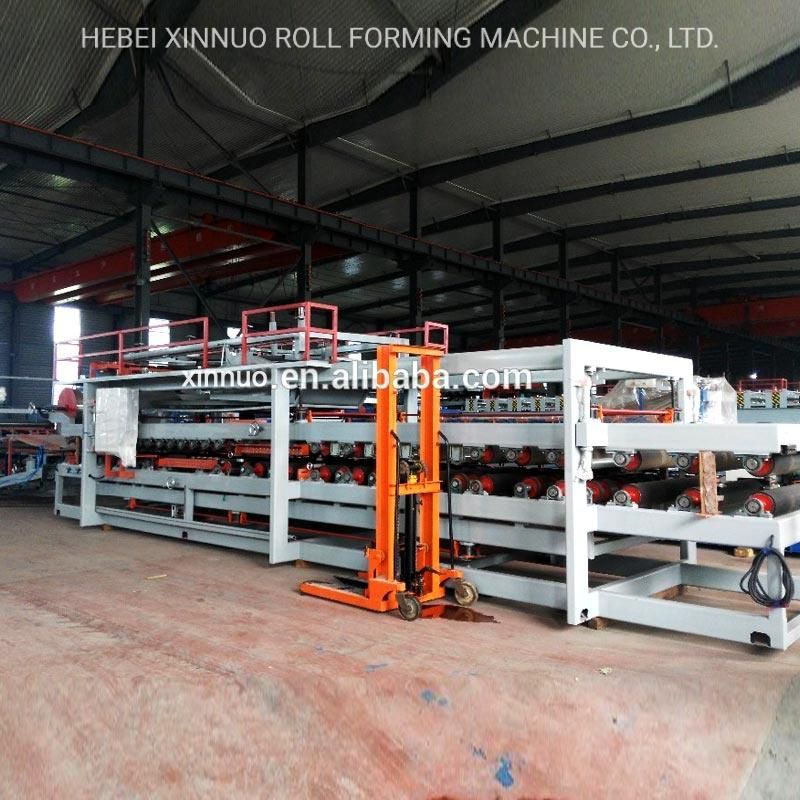
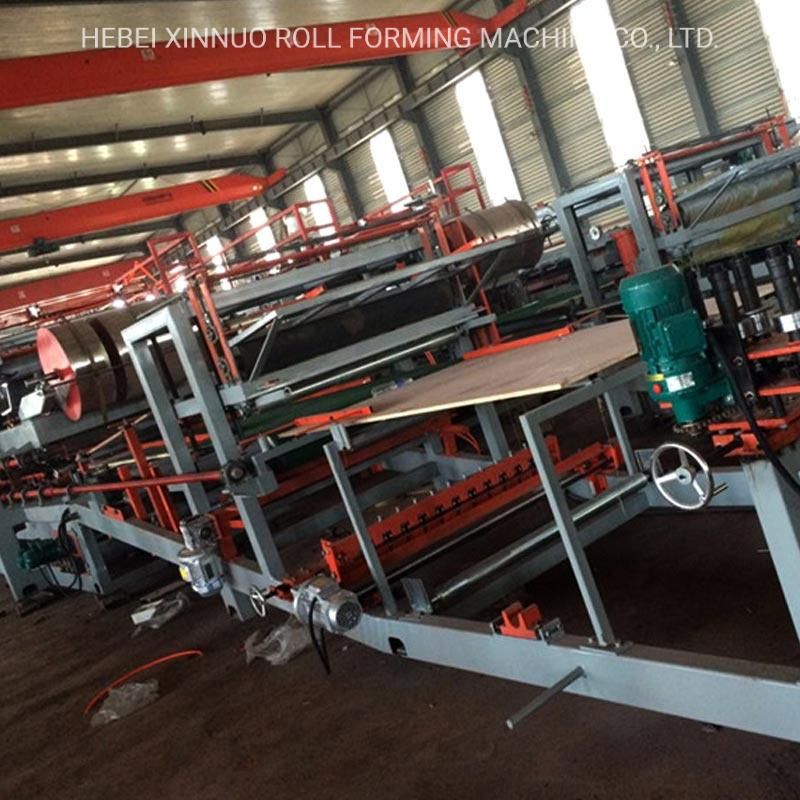
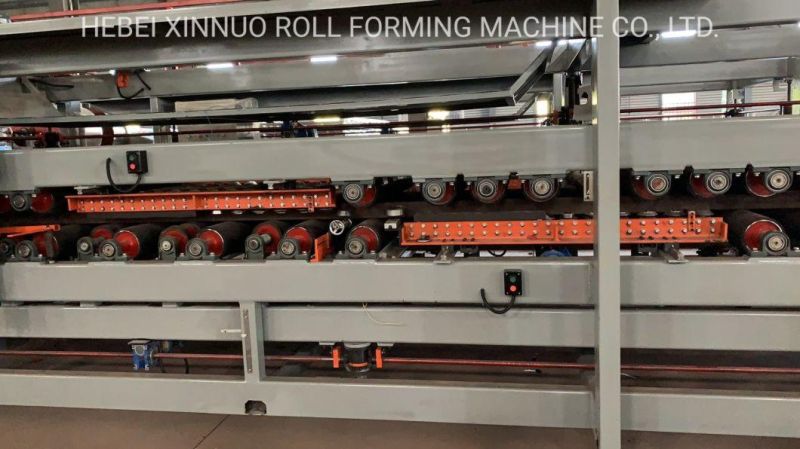
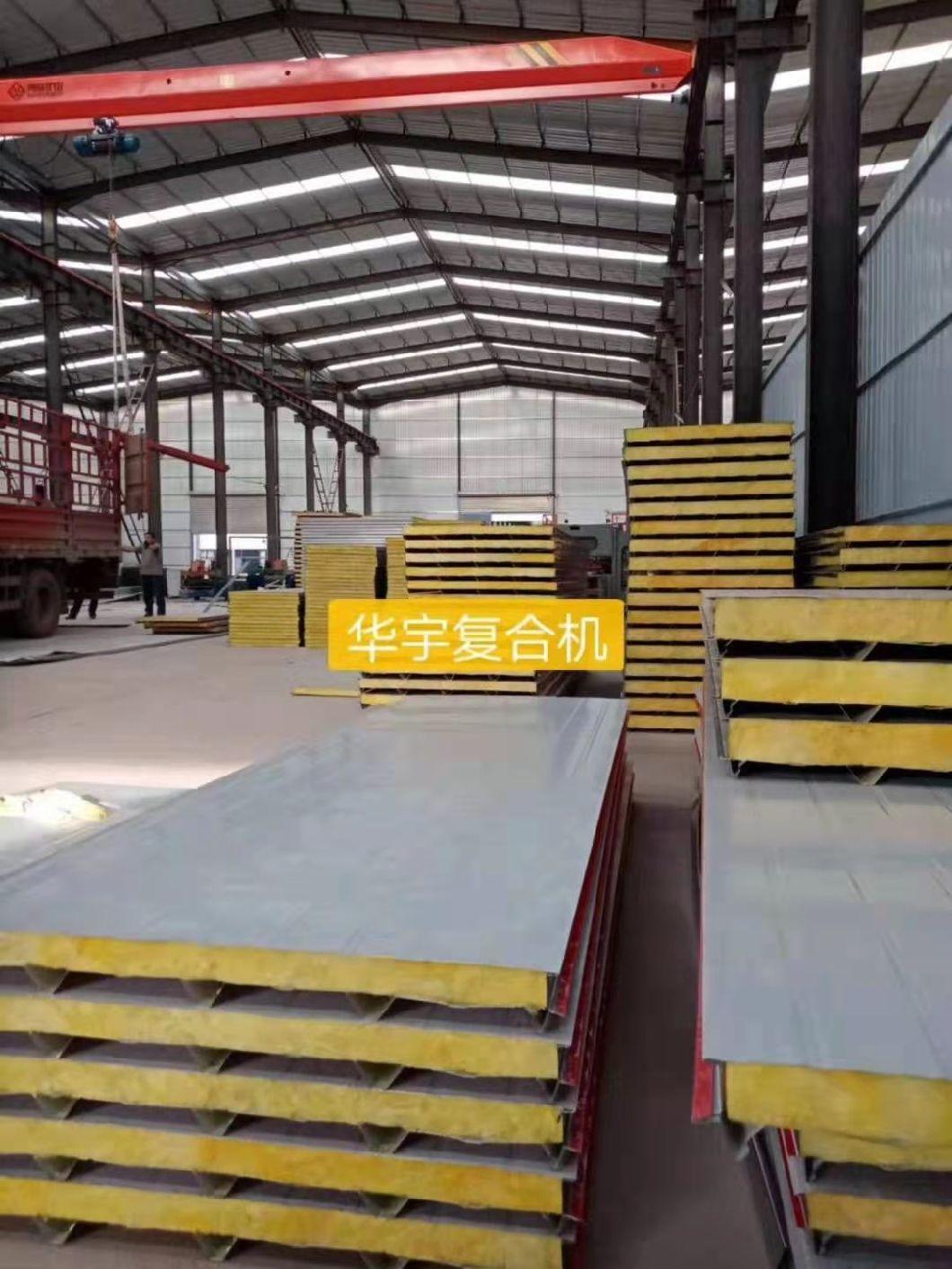
Our Advantages
Company Profile
