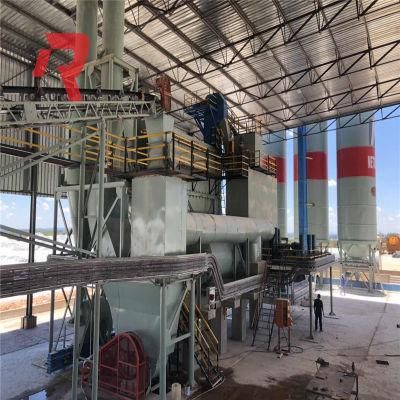
Large Capacity Phosphogypsum Powder Production Line
OYADE (Shandong) Machinery Equipment Co., Ltd.- Certification:ISO 9001:2008
- Control Type:PLC Control
- Crushing Degree:Fine Grinding Machine
- Automatic Grade:Automatic
- Raw Material:Fgd Gypsum ,Phosphogypsum ,Natural Gypsum
- Output:20000ton-500000ton,Year
Base Info
- Model NO.:YR-20190819A
- Technology:Hot Air Boling Furnace
- Advantages:Improve Quality , High Configuration
- Workers:4-6person
- Fuel:Gas ,Diesel ,Coal , Oil
- Automtic:PLC Control
- Lab Equipment:Available
- Dust Collector:Water Dust Removal , Bag Dust Collector Ect.
- Mill Machine:Ramond Mill , Vertical Mill , Ball Mill
- Transport Package:Bulk Packing
- Specification:30000ton to 500000ton ,year
- Trademark:Yurui
- Origin:Shandong Province
- HS Code:8474209000
- Production Capacity:100
Description
4)Scale thick: 78 ~ 85% adjustable.
Labor requirements
Unique advantage
this step can increase the gypsum liquidity .when it come to the boiling furnace ,it can easy to calcinate ,so we have this step
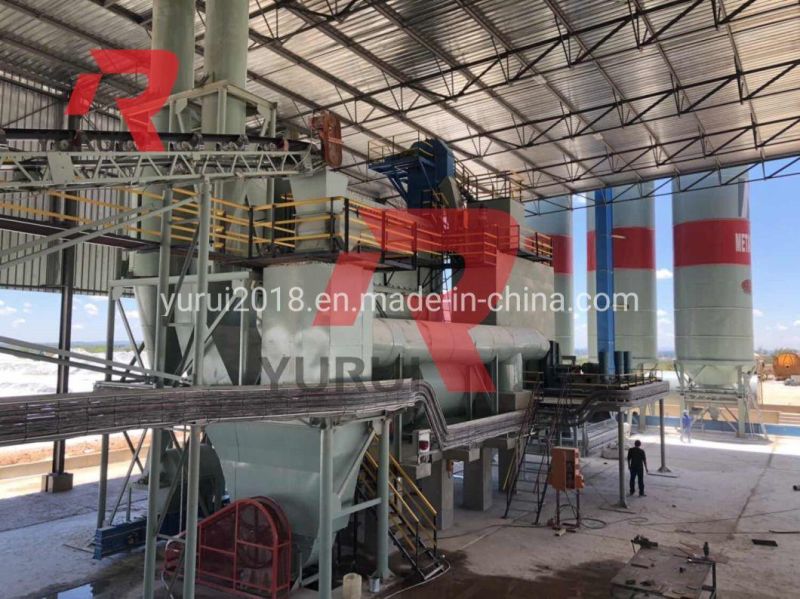
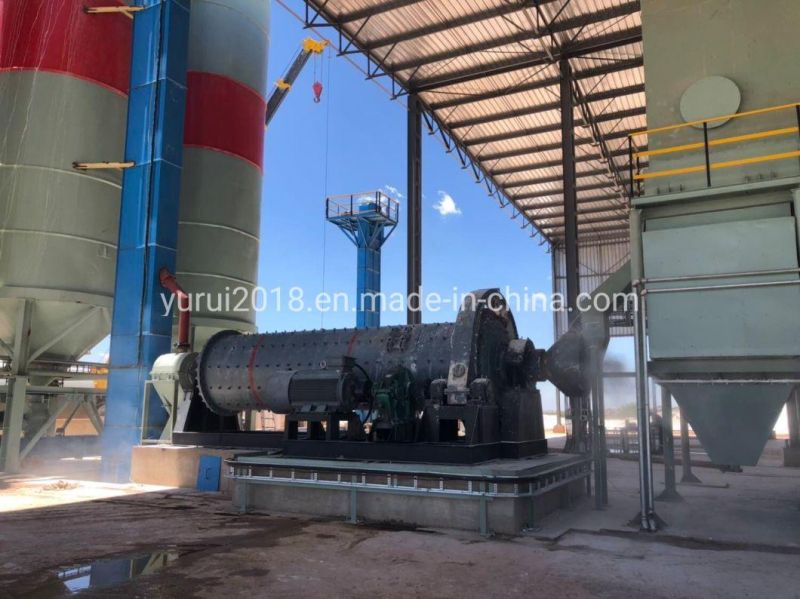
Technical data 1. The successful startup, short adjustment time, 15 days.
2. Natural gypsum and desulfurized gypsum not only can be calcined seperately but also
can calcine together.
3. Energy conservation, quality stability and controlable.Less passive downtime.
4. The natural gypsum can be controlled accurately, continuous and stable, and non-breakable
5. The equipment should be durable, easy to corrode the place to add protection, low maintenance and low labor intensity
6. The temperature of the cooked powder should be below 80 degrees.
7. Main motor use frequency converter, energy saving.
8. Less dust in the workshop and the control room is clear.
9. Designed production time to complete 200,000 tons of output within 10 months.
10. The equipment conforms to the relevant environmental protection, safety and other national rules , and the effect of dust removal can meet the national standards.
11. Anti-corrosion of the production line: the inside of the dust collector is embalmed, the cyclone is wear-resistant, the coal - fired furnace is scoured, hammer dryers remove iron and cache
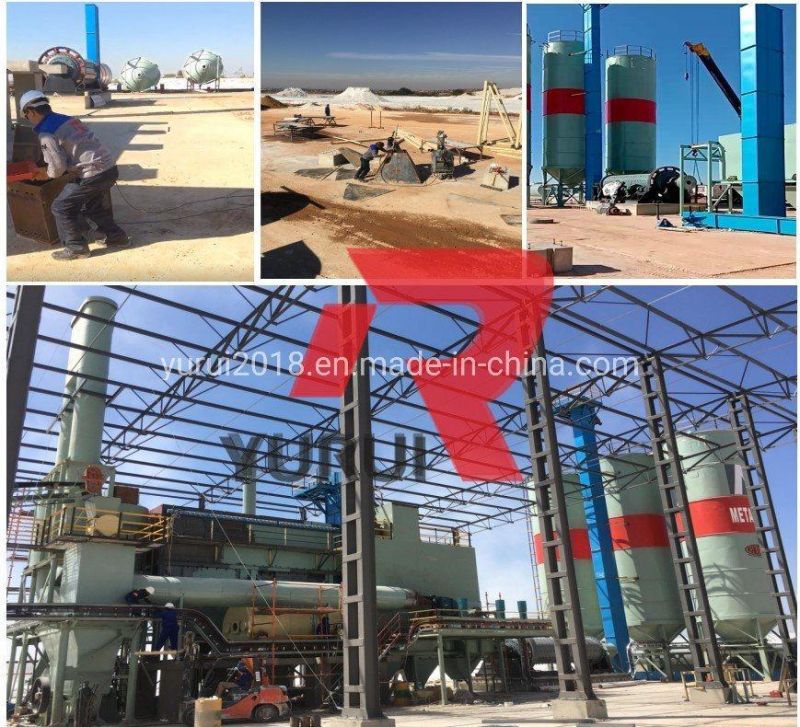
Technical feature
Our Service
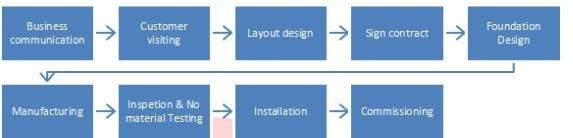
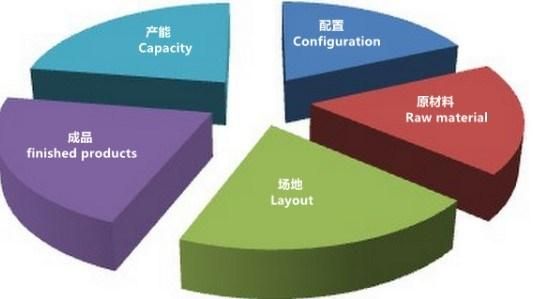
1)We will make the factory layout after the client got the final dimensions of the land.
2) After order confirm we will provide CAD foundation drawing for carrying on civil work, if necessary one civil engineer can be despatch to guide for civil work
3)Provide formula and production technology: Our engineers will adjust the formula according to your local raw material.
4)We will make commissioning and make training for worker until they occupy operate the equipment and produce qualified product
5)If necessary, we can arrange one engineer stay in your factory to guide production and management. And you only need to pay him a salary
6)After the completion of the project, we will continue to provide services to help customers purchase raw materials and accessories. If there is any problem in production, we will give customers a satisfactory answer within 24 hours. If necessary, we will arrange for engineers to help customers solve the problem on-site.
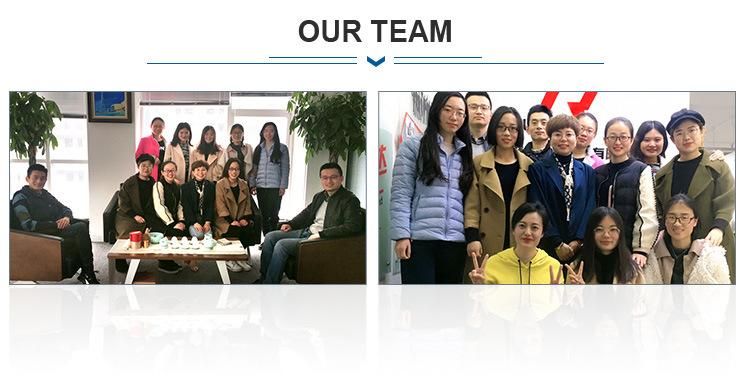
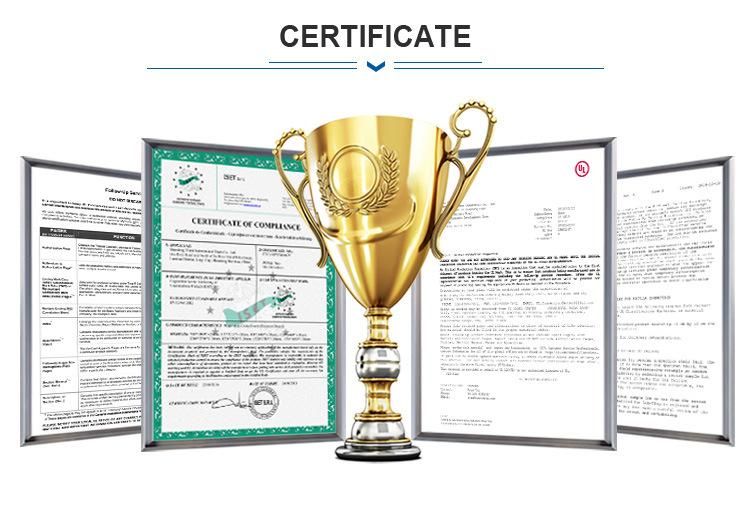
Labor requirements
From raw materials to drying | 1 person /8 hours |
Heating supply | 1 person /8 hours |
Calcinate control | 1 person /8 hours |
Electrical work | 1 person /12 hours |
Machine repair | 1 person /12 hours |
Unique advantage
1.Hammer drye
Function :The air dryer is used to bake the gypsum powder water containing less than 5% before entering the boiling furnace.this step can increase the gypsum liquidity .when it come to the boiling furnace ,it can easy to calcinate ,so we have this step
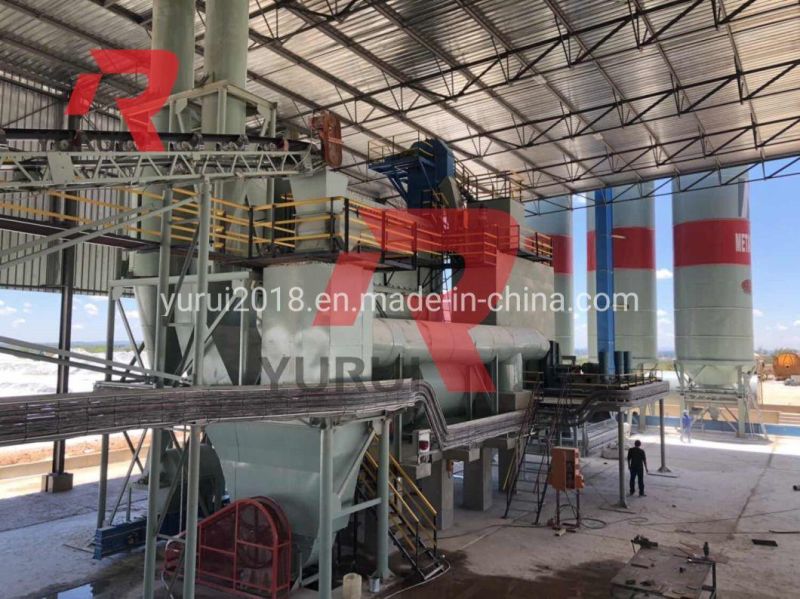
2.Ball Mill machine
Function :used to crush gypsum ore. Through the combined action of analysis machine and fan, this mill can meet the fineness of grinding requirements from different users.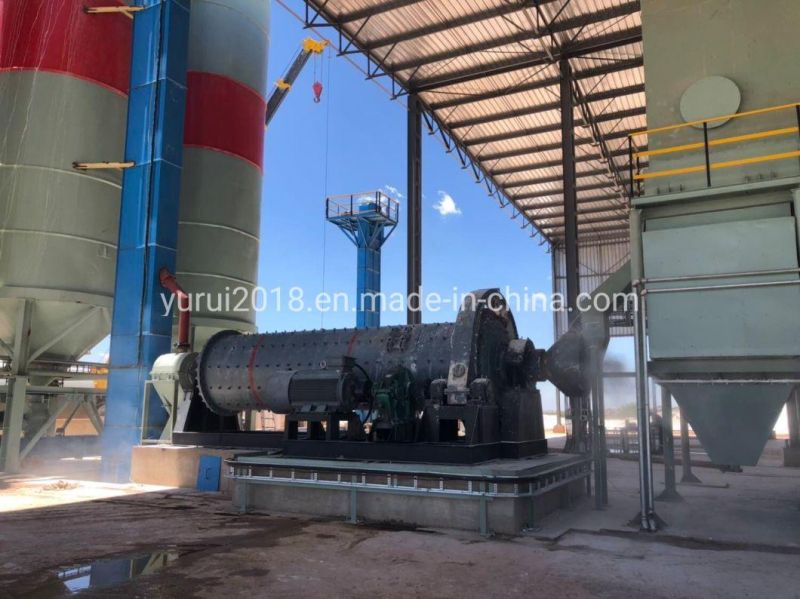
3.FD - chamber boiling furnace technology(hot iar )
The technology of FD - chamber boiling furnace technology can effectively prevent the mixing of raw materials with gypsum powder in the process of calcining .Traditional calcining technologies such as vertical boiling furnace , rotary kiln ,general boiling furnace, etc. Due to the effect of mixing function of the machinery and air flow, dihydrate gypsum ,semi-hydrated gypsum and anhydrite gypsum three-phase blending mutually in the process of boiling dehydration,It is inevitable that the phase composition of the final product will be polyphasic, and the product quality index will be reduced significantly.And FD - chamber fluid bed calcining process changes according to the temperature curve of gypsum powder , artificially divide the calcining process into four relatively independent dehydration space, effectively avoid the phenomenon of high and low-temperature material blending and the composition of the final product was improved.In the 1 and 2 areas of the main calcining furnace, high-temperature heat transfer technology is adopted to rapidly heat and dehydrate the materials that have just entered the FD- chamber boiling furnace, and slowly dehydrate in the 3 and 4 areas.Under the action of high pressure wind, the whole material presents a fluid boiling state, which improves the efficiency of heat transfer and mass transfer in gas and solid powder..2. Natural gypsum and desulfurized gypsum not only can be calcined seperately but also
can calcine together.
3. Energy conservation, quality stability and controlable.Less passive downtime.
4. The natural gypsum can be controlled accurately, continuous and stable, and non-breakable
5. The equipment should be durable, easy to corrode the place to add protection, low maintenance and low labor intensity
6. The temperature of the cooked powder should be below 80 degrees.
7. Main motor use frequency converter, energy saving.
8. Less dust in the workshop and the control room is clear.
9. Designed production time to complete 200,000 tons of output within 10 months.
10. The equipment conforms to the relevant environmental protection, safety and other national rules , and the effect of dust removal can meet the national standards.
11. Anti-corrosion of the production line: the inside of the dust collector is embalmed, the cyclone is wear-resistant, the coal - fired furnace is scoured, hammer dryers remove iron and cache
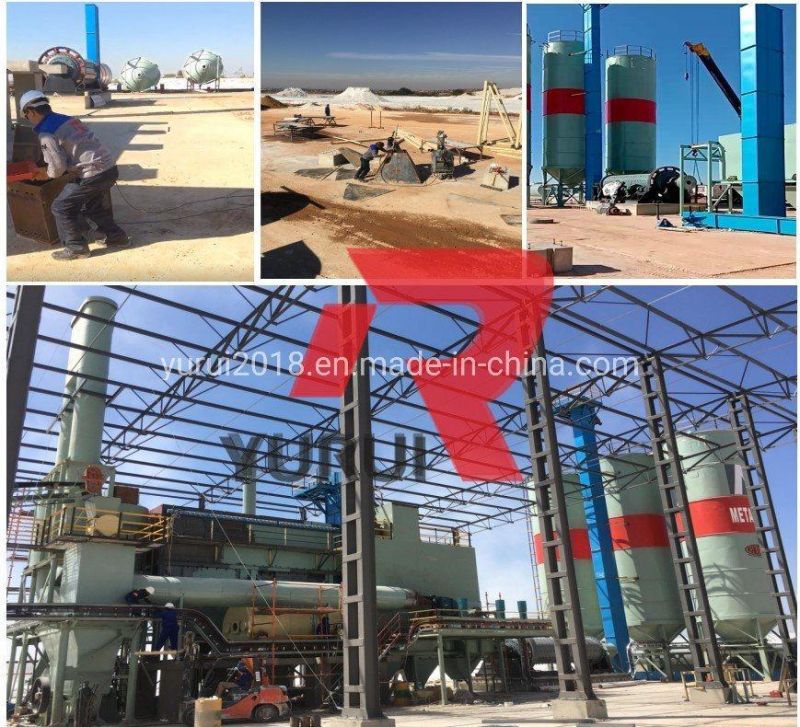
Technical feature
1 | Continuous production: using hammer dryer and soft start, |
2 | Quality stability: modification mill can increase the specific surface area of materials. |
3 | Energy conservation and stability: great brand frequency transformer |
4 | High performance of equipment: using bag dust collector, water bath desulfurization and denitration treatment, frequency transformer, Siemens electrical, PLC, guomao reducer, national standard cable, electrical control: ABB. |
5 | Easy control: Adpot computer display, PLC control. |
6 | Mature experience: The core features of our company are mature technologies that can provide a solid foundation for your company. |
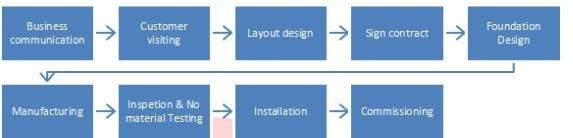
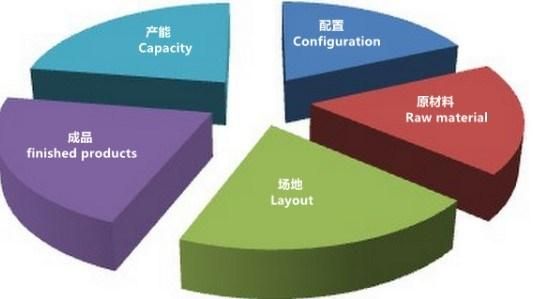
1)We will make the factory layout after the client got the final dimensions of the land.
2) After order confirm we will provide CAD foundation drawing for carrying on civil work, if necessary one civil engineer can be despatch to guide for civil work
3)Provide formula and production technology: Our engineers will adjust the formula according to your local raw material.
4)We will make commissioning and make training for worker until they occupy operate the equipment and produce qualified product
5)If necessary, we can arrange one engineer stay in your factory to guide production and management. And you only need to pay him a salary
6)After the completion of the project, we will continue to provide services to help customers purchase raw materials and accessories. If there is any problem in production, we will give customers a satisfactory answer within 24 hours. If necessary, we will arrange for engineers to help customers solve the problem on-site.
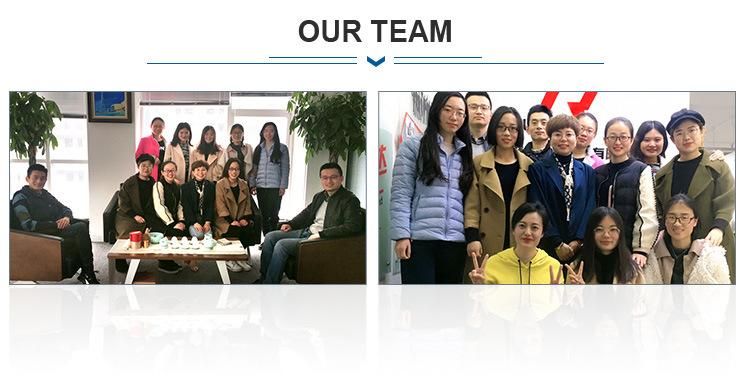
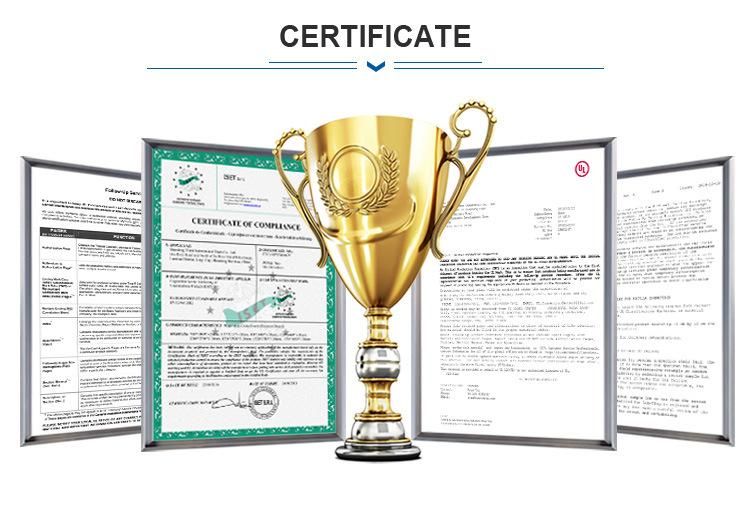